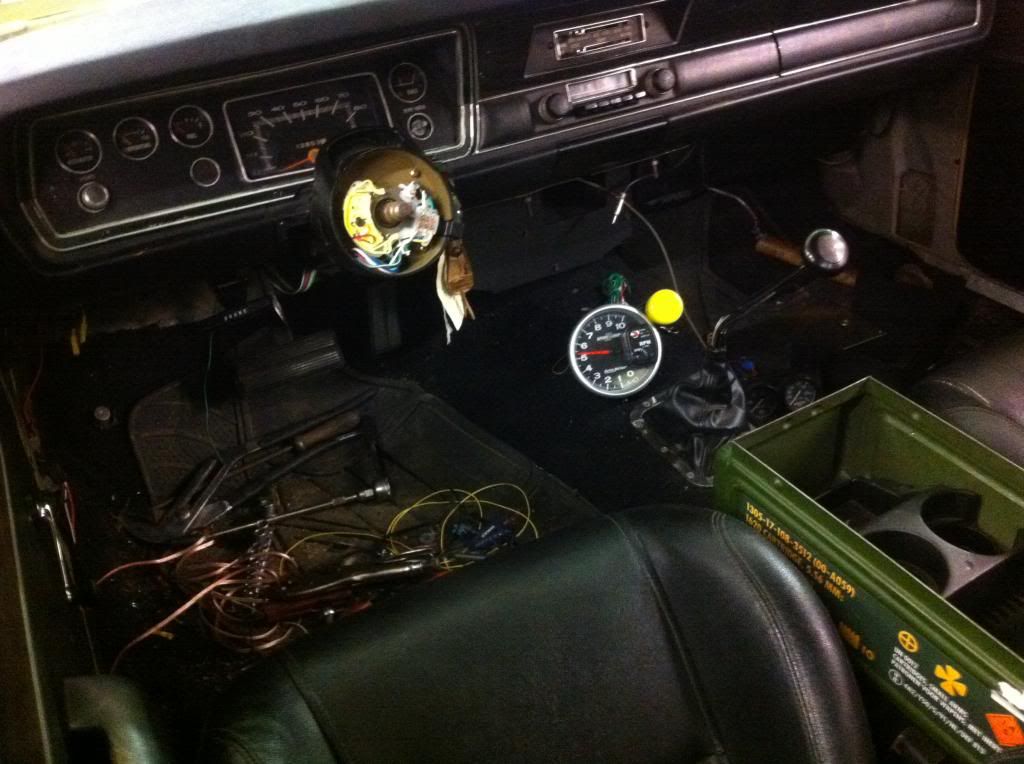
Johnny's Dart repairs
Moderator: Moderators
- Johnny Dart
- Posts: 850
- Joined: Tue Dec 24, 13 12:46 pm
- Location: East Sussex
- Johnny Dart
- Posts: 850
- Joined: Tue Dec 24, 13 12:46 pm
- Location: East Sussex
Fair play JD......A case of just jump in and get it done!!!! 

Dave Tildesley.....MMA-081
72 Dodge Dart
73 Plymouth Duster - SOLD
I wanna go so FAST i think i'm going to DIE!..........Then i'll shift into second!
"My Car is a work in progress, Probably never gonna get finished, never gonna have the money to Bananarama!!"
72 Dodge Dart
73 Plymouth Duster - SOLD
I wanna go so FAST i think i'm going to DIE!..........Then i'll shift into second!
"My Car is a work in progress, Probably never gonna get finished, never gonna have the money to Bananarama!!"
- Johnny Dart
- Posts: 850
- Joined: Tue Dec 24, 13 12:46 pm
- Location: East Sussex
I didn't take the dash pad off. I removed the steering wheel ,and undid the steering column bolts, and lowered it down, then removed the dash panel, to access the speedo cable and wires,cadboy wrote:I have a question JD, did you take out your Dash pad when you did this work?
If so can you give tell me how you got the bolts out as mine just keeps on turning and don't want to come out
The dash pad fixings are accessible from there, I guess yours must be turning in the pad.
- Johnny Dart
- Posts: 850
- Joined: Tue Dec 24, 13 12:46 pm
- Location: East Sussex
- Johnny Dart
- Posts: 850
- Joined: Tue Dec 24, 13 12:46 pm
- Location: East Sussex
- Johnny Dart
- Posts: 850
- Joined: Tue Dec 24, 13 12:46 pm
- Location: East Sussex
How are you going to narrow the axle? You need a jig to do it, and that means stripping out the diff. I don't know if you are aware of it, but the splines on the shafts are broached and hardened, cutting and resplining looses the hardness and you end up with a weaker shaft that stock, they tend to twist on the splined area, happened to me many years ago.
method that avoids using a jig
may not be big or clever
but ken who did it races quite a mean car, looks like crocodile dundee and appears to have no problems with anything much. possibly due to his free wheelin attitude or perhaps big knife
http://www.moparmarketforum.com/forum/v ... 46&t=21265
note he shortend his so he could use standard halfshafts from the same model axle form a much narrower car.
your axle is a US dana or Mopar axle
i found that splinage is governed by SAE. so 28 spline is 28 spline my 28 spline is the same a fords 28 spline which is the same a borg warners 28 spline and GMs 28 spline etc
whats your spline and what else uses your axle that is narrower than the jeep you got it from?
as long as the shortening you do fits with a left or right shaft from A-N-Other car and that work doesn't move the centre too far one way or the other from the middle of your off set tunnel. all is OK
notes
EB II is a ford falcon
the axle is a borg waner 78 in 28 spline
VE VF VG are aussie dodge darts/valiants
but its all the same stuff
before you start clamp a meter long ruler to each backing plate flange and measure the distance between them when facing front and back
then do it again once you are done
should, i think be a tiny smidge closer at the front
the variation between front and back should be the same before and afterwards.
you could do it up and down as well. but there shouldn't be any difference
axles shouldn't sag too much in the middle
depends on camber setting i suppose, but i'm not aware of the need for that at the back.
obvioulsy the longer and more ridgid your ruler is. the more accurate you will be in telling if you bent it in any way as you welded
see his notes on oil to the bearings... in theory you fill your diff to a height higher than the sleave you will use, so it shouldn't be a problem
but radius to the inner bore of the sleave at each end my help flow
and of course a taperd axle will move oil out to the ends by centrifugal force anyway
see notes on usuing bottle jack and a concrete beam or bridge and regarding honeing out the rough internal surface of the tube and forcing the parts together.
Dave
may not be big or clever
but ken who did it races quite a mean car, looks like crocodile dundee and appears to have no problems with anything much. possibly due to his free wheelin attitude or perhaps big knife

http://www.moparmarketforum.com/forum/v ... 46&t=21265
note he shortend his so he could use standard halfshafts from the same model axle form a much narrower car.
your axle is a US dana or Mopar axle
i found that splinage is governed by SAE. so 28 spline is 28 spline my 28 spline is the same a fords 28 spline which is the same a borg warners 28 spline and GMs 28 spline etc
whats your spline and what else uses your axle that is narrower than the jeep you got it from?
as long as the shortening you do fits with a left or right shaft from A-N-Other car and that work doesn't move the centre too far one way or the other from the middle of your off set tunnel. all is OK
notes
EB II is a ford falcon
the axle is a borg waner 78 in 28 spline
VE VF VG are aussie dodge darts/valiants
but its all the same stuff
before you start clamp a meter long ruler to each backing plate flange and measure the distance between them when facing front and back
then do it again once you are done
should, i think be a tiny smidge closer at the front
the variation between front and back should be the same before and afterwards.
you could do it up and down as well. but there shouldn't be any difference
axles shouldn't sag too much in the middle

obvioulsy the longer and more ridgid your ruler is. the more accurate you will be in telling if you bent it in any way as you welded
see his notes on oil to the bearings... in theory you fill your diff to a height higher than the sleave you will use, so it shouldn't be a problem
but radius to the inner bore of the sleave at each end my help flow
and of course a taperd axle will move oil out to the ends by centrifugal force anyway
see notes on usuing bottle jack and a concrete beam or bridge and regarding honeing out the rough internal surface of the tube and forcing the parts together.
Dave
The Greater Knapweed near the Mugwort by the Buckthorn tree is dying
- Johnny Dart
- Posts: 850
- Joined: Tue Dec 24, 13 12:46 pm
- Location: East Sussex
your axle is a US dana or Mopar axle
Dave[/quote]
Well Dave, the read of the post, is along the lines of what I will be attempting.
The axle I am using is a 30 spline Dana 44HD aluminium centre , like a Viper.
The first fopar I've made it to buy the wrong locker
I bought one for a Dana 44 and not a 44HD, and they are different item.
I now have bought another 44HD one
Ive had a measure up, and I need to cut 3 1/4 from one side and 3 3/4 from the other, that keeps the pinnion where it is on the car now.
I will cut them at work on a mechanical saw, and as the post, get my machine shop mate to machine some tube to fit inside the axle tube, plug weld though drilled holes and but weld and to the tube the other part.
making sure not to warp it by stitch welding opposite sides until complete weld.
My machinist mate, does axle shortening for race cars, what he does is cut the axle , make up a sleeve to go over the top, keyway the axle ends, and the sleeve, and weld the sleeve to the axle.
I'm not sure this would work on a RWD axle as the wheel bearing would have to go over the top if you needed to change the bearing.
So that might not work,
The other option is to buy a pair of cut to length axles from the states at about £120 each plus the rest.
How big is the wheel bearing hole compared to the axle diameter,need to check that out.
I back on normal days next week , so will have a think, also all input welcomed.
Dave[/quote]
Well Dave, the read of the post, is along the lines of what I will be attempting.
The axle I am using is a 30 spline Dana 44HD aluminium centre , like a Viper.
The first fopar I've made it to buy the wrong locker

I bought one for a Dana 44 and not a 44HD, and they are different item.
I now have bought another 44HD one

Ive had a measure up, and I need to cut 3 1/4 from one side and 3 3/4 from the other, that keeps the pinnion where it is on the car now.
I will cut them at work on a mechanical saw, and as the post, get my machine shop mate to machine some tube to fit inside the axle tube, plug weld though drilled holes and but weld and to the tube the other part.
making sure not to warp it by stitch welding opposite sides until complete weld.
My machinist mate, does axle shortening for race cars, what he does is cut the axle , make up a sleeve to go over the top, keyway the axle ends, and the sleeve, and weld the sleeve to the axle.
I'm not sure this would work on a RWD axle as the wheel bearing would have to go over the top if you needed to change the bearing.

So that might not work,
The other option is to buy a pair of cut to length axles from the states at about £120 each plus the rest.
How big is the wheel bearing hole compared to the axle diameter,need to check that out.
I back on normal days next week , so will have a think, also all input welcomed.

- Johnny Dart
- Posts: 850
- Joined: Tue Dec 24, 13 12:46 pm
- Location: East Sussex
I had a look in to getting the shafts re splined, but the re hardening was the stumbling block,as you say,it sort of points me at the cut to length shafts.Blue wrote:How are you going to narrow the axle? You need a jig to do it, and that means stripping out the diff. I don't know if you are aware of it, but the splines on the shafts are broached and hardened, cutting and resplining looses the hardness and you end up with a weaker shaft that stock, they tend to twist on the splined area, happened to me many years ago.
I 'll look into it a bit more next week.
i had a set of axles made by Moser
and transported here by Ron fenton STS see his post about a container load
takes moser 2 days to make axles 1-2 days to get them to florida where the container is
and rons container is here 1st week of April the shipping in the US was in dollars the same as what i paid ron in ££
obvioulsy rons costs depends on what he puts in his container so i doubt its the same price twice as that container needs to be filled to make it viable, but it was and allways has been a very reaonably priced and reliable and felxible service had 3 packages that way now
when the axles arrive regardless of how well youi measure they will be too long.
anything on the axle shaft will stop the oil from the centre spiraling out along the shafts to be delivered to the wheel bearings
if you need to borrow a case spreader let me know
just had one shipped. ex GM dealer never ben used for about an 8th the cost of a new one
you'd ned to make you adaptors up 2 plates to bolt to spreader that also bolt to the 2 cover bolt holes neares tha axles tubes unles yours has provision for a spreader mount
mind it weighs about 25 Kilos so pickup better than postage
Dave
and transported here by Ron fenton STS see his post about a container load
takes moser 2 days to make axles 1-2 days to get them to florida where the container is
and rons container is here 1st week of April the shipping in the US was in dollars the same as what i paid ron in ££
obvioulsy rons costs depends on what he puts in his container so i doubt its the same price twice as that container needs to be filled to make it viable, but it was and allways has been a very reaonably priced and reliable and felxible service had 3 packages that way now
when the axles arrive regardless of how well youi measure they will be too long.
anything on the axle shaft will stop the oil from the centre spiraling out along the shafts to be delivered to the wheel bearings
if you need to borrow a case spreader let me know
just had one shipped. ex GM dealer never ben used for about an 8th the cost of a new one
you'd ned to make you adaptors up 2 plates to bolt to spreader that also bolt to the 2 cover bolt holes neares tha axles tubes unles yours has provision for a spreader mount
mind it weighs about 25 Kilos so pickup better than postage
Dave
The Greater Knapweed near the Mugwort by the Buckthorn tree is dying
- Johnny Dart
- Posts: 850
- Joined: Tue Dec 24, 13 12:46 pm
- Location: East Sussex
you'd ned to make you adaptors up 2 plates to bolt to spreader that also bolt to the 2 cover bolt holes neares tha axles tubes unles yours has provision for a spreader mount
mind it weighs about 25 Kilos so pickup better than postage
Dave[/quote]
Thanks Dave,
I'm beginning to think I may have got the wrong (read more awkward ) axle. Unfortunately I didn't know at the time of purchase that there were Dana 44' s and Dana 44 HD's. Or that their parts are not interchangeable between the 44 and 44HD axles.
Anyway I will make this work. should get a bit more done next week ,so will report back then
mind it weighs about 25 Kilos so pickup better than postage
Dave[/quote]
Thanks Dave,
I'm beginning to think I may have got the wrong (read more awkward ) axle. Unfortunately I didn't know at the time of purchase that there were Dana 44' s and Dana 44 HD's. Or that their parts are not interchangeable between the 44 and 44HD axles.
Anyway I will make this work. should get a bit more done next week ,so will report back then